
PP MicroPile
ข้อมูลข่าวสาร สาระน่ารู้เรื่องบ้าน บ้านแข็งแรง มั่นคงด้วยเสาเข็มไมโครไพล์ มารู้จัก…เสาเข็มไมโครไพล์

PP MicroPile
ข้อมูลข่าวสาร สาระน่ารู้เรื่องบ้าน บ้านแข็งแรง มั่นคงด้วยเสาเข็มไมโครไพล์ มารู้จัก…เสาเข็มไมโครไพล์
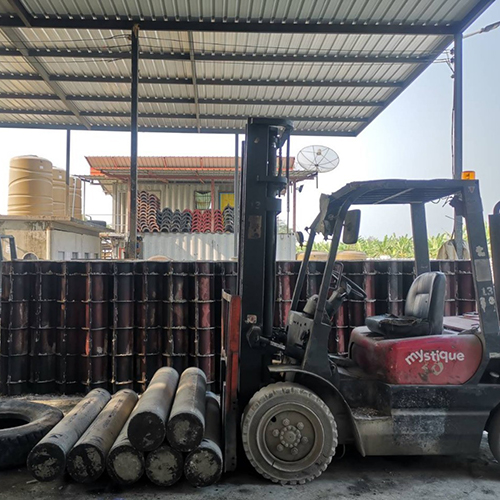
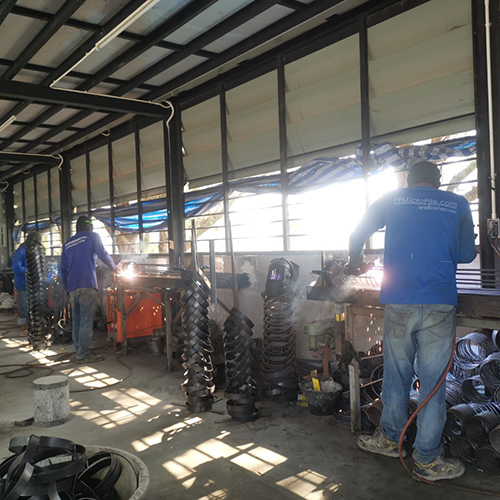
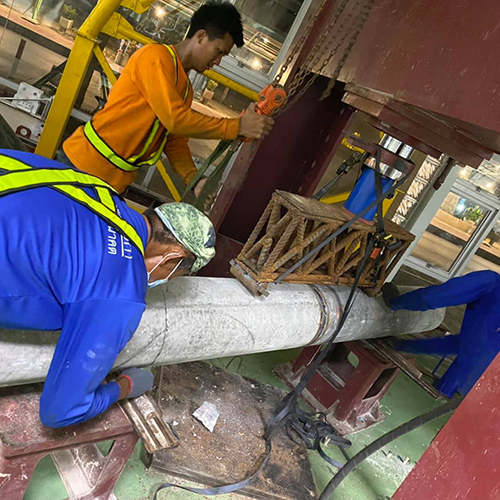
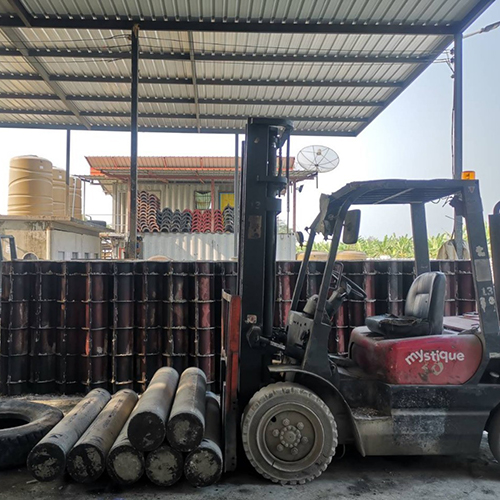
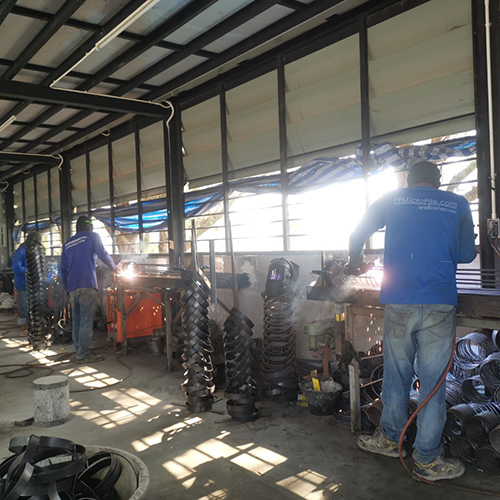
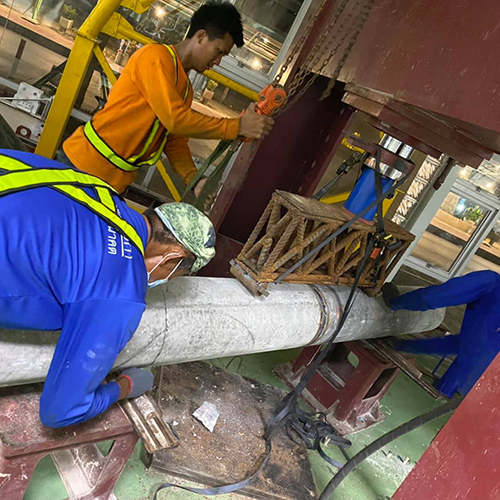
12 หลักในการออกแบบรอยเชื่อม
12 หลักในการออกแบบรอยเชื่อม
ข้อที่ 7 welded connection ที่ดีจะต้อง.
คำนึงถึง detail ที่ส่วนปลายของการเชื่อมเสมอ โดยเฉพาะเรื่องของการเว้นรอยเชื่อมจากส่วนปลายขอบของชิ้นส่วน Connection นั้นๆ ซึ่งเราจะพบ 2 กรณีที่เจอบ่อย ๆ ตามนี้
– ในโครงสร้างแบบ Truss ที่ Member ชิ้นนั้นรับแรงดึงแล้วมีชิ้น Diagonal มาต่อเข้ากันด้วยวิธีการเชื่อมแบบ Fillet Weld (ตามรูปด้านซ้ายของหน้า 9) ในกรณีเราจะเห็นว่าหากเราทำการเชื่อมยาวไปจนถึงส่วนขอบบนของชิ้นส่วนรับแรงดึงนี้ด้วยความร้อนในการเชื่อมจะทำให้บริเวณดังกล่าวเกิดเป็นรอย (notch) ขึ้น ทำให้ชิ้นงานออกมาเรียกได้ว่า “น่าเกลียด” ดังนั้นสิ่งที่เราทำได้ก็คือเว้นระยะจากส่วนปลายของรอยเชื่อมกับส่วนขอบบนนี้ซักหน่อยเพื่อไม่ให้เกิดรอยขึ้น ระยะเว้นตรงนี้ภาษาสากลเค้าจะเรียกกันว่า “Holdback” นะครับ
– อีกกรณีจะเป็นเรื่องของการยอมให้เกิด Relative Deformation ระหว่างชิ้นส่วน ยกตัวอย่างการเชื่อมแผ่น Stiffener ที่ Web (ตามรูปด้านขวาของหน้า 9) ของคานหากเราเชื่อมตลอดทั้งความยาวของแผ่น Stiffener โดยเว้นระยะไว้เพียงน้อยมาก (น้อยเกินไป) และเนื่องจากส่วนของ Web ที่ไม่ได้โดนเชื่อมกับแผ่น Stiffener ที่เหลือน้อยนี้อาจทำให้เกิด Deformation ขึ้นระหว่างการขนส่งได้ (Stiffness มันน้อยกว่าส่วนที่โดนเชื่อมเลยเกิด Deformation ขึ้นบริเวณนี้) และท้ายที่สุดอาจจะเกิด Fatigue Crack ขึ้นได้ ดังนั้นวิธีการแก้ปัญหาของเราก็เหมือนเดิมเลยคือเว้นระยะของรอยเชื่อมที่เราเชื่อมตามยาวของแผ่น Stiffener ไว้ให้พอเหมาะซักหน่อย โดย AISC กำหนดระยะเว้นไว้ที่ระยะมากกว่า 4 เท่าของความหนา Web แต่ไม่เกิน 6 เท่าของความหนา Web
**หมายเหตุ การเว้นระยะดังกล่าวนี้ AISC บอกว่าผู้ออกแบบสามารถมองข้ามเรื่องของกำลังที่อาจจะน้อยลงได้เลย
ข้อที่ 8 welded connection ที่ดีจะต้อง …
มีการออกแบบให้ช่างเชื่อมนั้นทำงานได้ง่าย มองเผินๆ อาจจะ Common Sense ไปหน่อยแต่ถ้าดูกันจริงๆ แล้วมันส่งผลต่อคุณภาพในการเชื่อมของเราไม่มากก็น้อยเลย ซึ่งการที่จะให้ช่างเชื่อมได้ง่ายนั้นก็คือต้องมีช่องว่างมากพอที่จะให้ช่างเชื่อมนั้นเห็นการเชื่อมของตนได้ ขยายความการมองเห็นการเชื่อมก็คือช่างเชื่อมจะต้องมองส่วนที่เรียกว่า “บ่อละลาย” หรือ “Puddle” นั่นเอง (ในการเชื่อมทุกครั้งต้องใช้เปลวไฟเผาชิ้นงานบริเวณแนวที่จะเชื่อมจนร้อนหลอมละลายเป็นแอ่งกลมหรือที่เรียกว่าบ่อละลาย หรือ Puddle ซึ่งเป็นส่วนที่ร้อนที่สุดหลังจากนั้นให้ส่ายหัวเชื่อมเล็กน้อยเพื่อให้ความร้อนแก่ชิ้นงานได้อย่างทั่วถึง เมื่อชิ้นงานหลอมละลายเป็นบ่อละลายแล้วจึงเติมลวดเชื่อมลงไปเป็นตัวประสานชิ้นงาน)
ข้อที่ 9 welded connection ที่ดีจะต้อง …
มีการเลือกประเภทของรอยต่อและการเชื่อมให้เหมาะสมกับลักษณะของแรงที่กระทำชิ้นส่วนนั้น ๆ ยกตัวอย่าง Connection ที่มาต่อกันแบบ Butt Joint โดยเชื่อม 2 ชิ้นเข้าด้วยรอยเชื่อมแบบ PJP Groove Weld (ตามหน้าที่ 11) จะเห็นว่าหาก Connection ดังกล่าวนี้รับแรงดึงจะถูกจัดประเภทว่าเป็น Connection ที่ “แย่” รอยเชื่อมจะไปทำให้ Centroid เปลี่ยนจุดทำให้แรงดึงไม่ผ่านจุด Centroid นี้และทำให้เกิด Rotation ขึ้น ในทางกลับกันถ้าหากนำ Connection ดังกล่าวนี้มารับแรงอัดก็ไม่เกิดปัญหาดังกล่าวนี้ซึ่งจัดได้ว่าเป็น Connection ที่ “ดี”
ข้อที่ 10 welded connection ที่ดีจะต้อง …
คำนึงถึงคุณสมบัติของวัสดุเหล็กบางประการที่อาจจะส่งผลต่อคุณภาพของการเชื่อมได้ ในที่นี้จะยกตัวอย่างคุณสมบัติหนึ่งที่ส่งผลโดยตรงเลยคือคุณสมบัติ “Thickness Ductility”…ก่อนอื่นเราต้องมองย้อนถึงกระบวนการในการผลิตเหล็กก่อนเลย หลายท่านอาจจะยังไม่รู้ว่าเหล็กรูปพรรณที่เราใช้กันนี้มันต้องมีการผ่านกระบวนการของการรีดเหล็กมาก่อน และต้องบอกทุกท่านว่าในเหล็กที่เอามาใช้มันจะมีพวกสารปนเปื้อนติดมาเสมอ ในทางอุตสาหกรรมเค้าจะเรียกกันว่า “Inclusion” เมื่อเหล็กผ่านกระบวนการรีดดังกล่าวสารปนเปื้อนเหล่านี้ก็จะกระจายอยู่ทั่วแผ่นเหล็กที่รีดออกมาซึ่งส่วนมากจะกระจายอยู่ใกล้กับผิวของแผ่นเหล็ก ใช่ครับอย่างที่ทุกท่านคิด…Inclusion มันจะส่งผลต่อคุณสมบัติ (Properties) ของเหล็ก และคุณสมบัติที่โดนผลกระทบนี้โดยตรงก็คือ Ductility ในทิศทางความหนาของเหล็กนั่นเอง ท้ายสุดเมื่อนำเหล็กแผ่นที่ได้จากการรีดแต่ละชิ้นมาเชื่อมกันเป็นเหล็กรูปพรรณ ยกตัวอย่างนำเหล็กแผ่น 4 ชิ้นเชื่อมเข้ากันแบบ Filet Weld ประกอบเป็นเหล็กกล่อง (HSS) เมื่อความร้อนจากการเชื่อมลดลงจะทำให้เกิดการหดตัวเนื่องจากความเย็นของวัสดุเชื่อม ทำให้เกิดแรงดึงขึ้นและไปดึงเหล็กแผ่นที่นำมาประกอบในทิศทางของความหนาซึ่งอาจทำให้เกิดการแตกร้าวได้!!!
ข้อที่ 11 welded connection ที่ดีจะต้อง …
คำนึงถึงความคลาดเคลื่อนของชิ้นงานและความเป็นไปได้ในการติดตั้ง ทุกครั้งที่มาการนำมาชิ้นงานมาใช้และมาติดตั้งจะต้องมีการตรวจสอบที่เรียกว่าความคลาดเคลื่อน หรือ Tolerance ก่อนเสมอ คำว่าความคลาดเคลื่อนในที่นี้จะประกอบไปด้วย 1. ความคลาดเคลื่อนจากชิ้นงาน (อ้างอิงค่าความคลาดเคลื่อนที่ยอมให้จาก ASTM) 2. ความคลาดเคลื่อนจากการติดตั้ง (อ้างอิงค่าความคลาดเคลื่อนที่ยอมให้จาก AWS) หลายครั้งเมื่อคำนวณค่าความคลาดเคลื่อนที่ยอมให้ทั้งสองออกมาค่าความคลาดเคลื่อนที่ยอมให้จากการติดตั้งจะมากกว่าความคลาดเคลื่อนจากชิ้นงาน ทำให้บางครั้งเมื่อมีชิ้นส่วนที่มีความคลาดเคลื่อนของชิ้นงานที่มาก 2 ชิ้นมาต่อเข้าด้วยกันอาจจะทำให้เกิดค่าความคลาดเคลื่อนของการติดตั้งเกินจาก Limit ที่กำหนดไว้ก็เป็นได้
ข้อ 12 welded connection ที่ดีจะต้อง …
ออกแบบโดยคำนึงถึงความประหยัดแต่ต้องอยู่บนพื้นฐานของความปลอดภัย หลายครั้งที่ Option ที่ถูกกว่าจะมีวิธีการทำงานที่ยากและอาจทำให้เกิดอันตรายได้ ดังนั้นวิศวกรควรจะคำนึงถึงวิธี/ขั้นตอนในการทำงานที่ง่ายและปลอดภัย ตามรูปตัวอย่างหน้า 14 เลย
ข้อที่ 7 welded connection ที่ดีจะต้อง.
คำนึงถึง detail ที่ส่วนปลายของการเชื่อมเสมอ โดยเฉพาะเรื่องของการเว้นรอยเชื่อมจากส่วนปลายขอบของชิ้นส่วน Connection นั้นๆ ซึ่งเราจะพบ 2 กรณีที่เจอบ่อย ๆ ตามนี้
– ในโครงสร้างแบบ Truss ที่ Member ชิ้นนั้นรับแรงดึงแล้วมีชิ้น Diagonal มาต่อเข้ากันด้วยวิธีการเชื่อมแบบ Fillet Weld (ตามรูปด้านซ้ายของหน้า 9) ในกรณีเราจะเห็นว่าหากเราทำการเชื่อมยาวไปจนถึงส่วนขอบบนของชิ้นส่วนรับแรงดึงนี้ด้วยความร้อนในการเชื่อมจะทำให้บริเวณดังกล่าวเกิดเป็นรอย (notch) ขึ้น ทำให้ชิ้นงานออกมาเรียกได้ว่า “น่าเกลียด” ดังนั้นสิ่งที่เราทำได้ก็คือเว้นระยะจากส่วนปลายของรอยเชื่อมกับส่วนขอบบนนี้ซักหน่อยเพื่อไม่ให้เกิดรอยขึ้น ระยะเว้นตรงนี้ภาษาสากลเค้าจะเรียกกันว่า “Holdback” นะครับ
– อีกกรณีจะเป็นเรื่องของการยอมให้เกิด Relative Deformation ระหว่างชิ้นส่วน ยกตัวอย่างการเชื่อมแผ่น Stiffener ที่ Web (ตามรูปด้านขวาของหน้า 9) ของคานหากเราเชื่อมตลอดทั้งความยาวของแผ่น Stiffener โดยเว้นระยะไว้เพียงน้อยมาก (น้อยเกินไป) และเนื่องจากส่วนของ Web ที่ไม่ได้โดนเชื่อมกับแผ่น Stiffener ที่เหลือน้อยนี้อาจทำให้เกิด Deformation ขึ้นระหว่างการขนส่งได้ (Stiffness มันน้อยกว่าส่วนที่โดนเชื่อมเลยเกิด Deformation ขึ้นบริเวณนี้) และท้ายที่สุดอาจจะเกิด Fatigue Crack ขึ้นได้ ดังนั้นวิธีการแก้ปัญหาของเราก็เหมือนเดิมเลยคือเว้นระยะของรอยเชื่อมที่เราเชื่อมตามยาวของแผ่น Stiffener ไว้ให้พอเหมาะซักหน่อย โดย AISC กำหนดระยะเว้นไว้ที่ระยะมากกว่า 4 เท่าของความหนา Web แต่ไม่เกิน 6 เท่าของความหนา Web
**หมายเหตุ การเว้นระยะดังกล่าวนี้ AISC บอกว่าผู้ออกแบบสามารถมองข้ามเรื่องของกำลังที่อาจจะน้อยลงได้เลย
ข้อที่ 8 welded connection ที่ดีจะต้อง …
มีการออกแบบให้ช่างเชื่อมนั้นทำงานได้ง่าย มองเผินๆ อาจจะ Common Sense ไปหน่อยแต่ถ้าดูกันจริงๆ แล้วมันส่งผลต่อคุณภาพในการเชื่อมของเราไม่มากก็น้อยเลย ซึ่งการที่จะให้ช่างเชื่อมได้ง่ายนั้นก็คือต้องมีช่องว่างมากพอที่จะให้ช่างเชื่อมนั้นเห็นการเชื่อมของตนได้ ขยายความการมองเห็นการเชื่อมก็คือช่างเชื่อมจะต้องมองส่วนที่เรียกว่า “บ่อละลาย” หรือ “Puddle” นั่นเอง (ในการเชื่อมทุกครั้งต้องใช้เปลวไฟเผาชิ้นงานบริเวณแนวที่จะเชื่อมจนร้อนหลอมละลายเป็นแอ่งกลมหรือที่เรียกว่าบ่อละลาย หรือ Puddle ซึ่งเป็นส่วนที่ร้อนที่สุดหลังจากนั้นให้ส่ายหัวเชื่อมเล็กน้อยเพื่อให้ความร้อนแก่ชิ้นงานได้อย่างทั่วถึง เมื่อชิ้นงานหลอมละลายเป็นบ่อละลายแล้วจึงเติมลวดเชื่อมลงไปเป็นตัวประสานชิ้นงาน)
ข้อที่ 9 welded connection ที่ดีจะต้อง …
มีการเลือกประเภทของรอยต่อและการเชื่อมให้เหมาะสมกับลักษณะของแรงที่กระทำชิ้นส่วนนั้น ๆ ยกตัวอย่าง Connection ที่มาต่อกันแบบ Butt Joint โดยเชื่อม 2 ชิ้นเข้าด้วยรอยเชื่อมแบบ PJP Groove Weld (ตามหน้าที่ 11) จะเห็นว่าหาก Connection ดังกล่าวนี้รับแรงดึงจะถูกจัดประเภทว่าเป็น Connection ที่ “แย่” รอยเชื่อมจะไปทำให้ Centroid เปลี่ยนจุดทำให้แรงดึงไม่ผ่านจุด Centroid นี้และทำให้เกิด Rotation ขึ้น ในทางกลับกันถ้าหากนำ Connection ดังกล่าวนี้มารับแรงอัดก็ไม่เกิดปัญหาดังกล่าวนี้ซึ่งจัดได้ว่าเป็น Connection ที่ “ดี”
ข้อที่ 10 welded connection ที่ดีจะต้อง …
คำนึงถึงคุณสมบัติของวัสดุเหล็กบางประการที่อาจจะส่งผลต่อคุณภาพของการเชื่อมได้ ในที่นี้จะยกตัวอย่างคุณสมบัติหนึ่งที่ส่งผลโดยตรงเลยคือคุณสมบัติ “Thickness Ductility”…ก่อนอื่นเราต้องมองย้อนถึงกระบวนการในการผลิตเหล็กก่อนเลย หลายท่านอาจจะยังไม่รู้ว่าเหล็กรูปพรรณที่เราใช้กันนี้มันต้องมีการผ่านกระบวนการของการรีดเหล็กมาก่อน และต้องบอกทุกท่านว่าในเหล็กที่เอามาใช้มันจะมีพวกสารปนเปื้อนติดมาเสมอ ในทางอุตสาหกรรมเค้าจะเรียกกันว่า “Inclusion” เมื่อเหล็กผ่านกระบวนการรีดดังกล่าวสารปนเปื้อนเหล่านี้ก็จะกระจายอยู่ทั่วแผ่นเหล็กที่รีดออกมาซึ่งส่วนมากจะกระจายอยู่ใกล้กับผิวของแผ่นเหล็ก ใช่ครับอย่างที่ทุกท่านคิด…Inclusion มันจะส่งผลต่อคุณสมบัติ (Properties) ของเหล็ก และคุณสมบัติที่โดนผลกระทบนี้โดยตรงก็คือ Ductility ในทิศทางความหนาของเหล็กนั่นเอง ท้ายสุดเมื่อนำเหล็กแผ่นที่ได้จากการรีดแต่ละชิ้นมาเชื่อมกันเป็นเหล็กรูปพรรณ ยกตัวอย่างนำเหล็กแผ่น 4 ชิ้นเชื่อมเข้ากันแบบ Filet Weld ประกอบเป็นเหล็กกล่อง (HSS) เมื่อความร้อนจากการเชื่อมลดลงจะทำให้เกิดการหดตัวเนื่องจากความเย็นของวัสดุเชื่อม ทำให้เกิดแรงดึงขึ้นและไปดึงเหล็กแผ่นที่นำมาประกอบในทิศทางของความหนาซึ่งอาจทำให้เกิดการแตกร้าวได้!!!
ข้อที่ 11 welded connection ที่ดีจะต้อง …
คำนึงถึงความคลาดเคลื่อนของชิ้นงานและความเป็นไปได้ในการติดตั้ง ทุกครั้งที่มาการนำมาชิ้นงานมาใช้และมาติดตั้งจะต้องมีการตรวจสอบที่เรียกว่าความคลาดเคลื่อน หรือ Tolerance ก่อนเสมอ คำว่าความคลาดเคลื่อนในที่นี้จะประกอบไปด้วย 1. ความคลาดเคลื่อนจากชิ้นงาน (อ้างอิงค่าความคลาดเคลื่อนที่ยอมให้จาก ASTM) 2. ความคลาดเคลื่อนจากการติดตั้ง (อ้างอิงค่าความคลาดเคลื่อนที่ยอมให้จาก AWS) หลายครั้งเมื่อคำนวณค่าความคลาดเคลื่อนที่ยอมให้ทั้งสองออกมาค่าความคลาดเคลื่อนที่ยอมให้จากการติดตั้งจะมากกว่าความคลาดเคลื่อนจากชิ้นงาน ทำให้บางครั้งเมื่อมีชิ้นส่วนที่มีความคลาดเคลื่อนของชิ้นงานที่มาก 2 ชิ้นมาต่อเข้าด้วยกันอาจจะทำให้เกิดค่าความคลาดเคลื่อนของการติดตั้งเกินจาก Limit ที่กำหนดไว้ก็เป็นได้
ข้อ 12 welded connection ที่ดีจะต้อง …
ออกแบบโดยคำนึงถึงความประหยัดแต่ต้องอยู่บนพื้นฐานของความปลอดภัย หลายครั้งที่ Option ที่ถูกกว่าจะมีวิธีการทำงานที่ยากและอาจทำให้เกิดอันตรายได้ ดังนั้นวิศวกรควรจะคำนึงถึงวิธี/ขั้นตอนในการทำงานที่ง่ายและปลอดภัย ตามรูปตัวอย่างหน้า 14 เลย
ที่มา Facebook: @welovesteelconstruction Part1, Part2
12 หลักในการออกแบบรอยเชื่อม
12 หลักในการออกแบบรอยเชื่อม
บริษัท พีพี ไมโครไพล์ จำกัด (สำนักงานใหญ่)
50 ม.1 ตำบลบางเตย อำเภอสามโคก จังหวัดปทุมธานี 12160
สำนักงาน: 02 039 7596 โทรสาร: 02 977 3522
โทร: 081 357 2199
PPmicropile@gmail.com